AWP Conference 2024

PTAG is proud to be a Gold Sponsor of the 16th Annual Global AWP Conference, which will be held in Houston, Texas, on October 7 and 8, 2024. The event will take place at the Royal Sonesta Houston and will bring together over 400 key construction stakeholders and leaders from around the world.
What is the Global AWP Conference?
The Annual AWP Conference is the premier event for construction professionals dedicated to improving project outcomes through the adoption and implementation of Advanced Work Packaging (AWP). The conference provides a platform for practitioners involved in designing, planning, and executing construction projects to exchange insights, explore cutting-edge innovations, and discuss best practices that enhance efficiency and effectiveness across the industry.
Why Attend?
As a key event for the global construction industry, the AWP Conference offers unparalleled opportunities to:
- Engage in In-Depth Discussions: Participate in discussions on critical topics such as project flow, data management, material management, and the comprehensive implementation of AWP.
- Learn from Experts: Attend presentations by subject matter experts who will share the latest innovations and advancements in technology, data utilization, and software solutions that are driving the future of construction.
- Expand Your Network: Network with a diverse community of owners, contractors, and consultants who are leading the way in AWP implementation and construction excellence.
Whether you are a seasoned AWP practitioner or new to the field, there are learning opportunities for everyone. The conference will offer a free AWP overview course, as well as a discounted fundamentals course, ensuring that all attendees can enhance their knowledge and skills, regardless of experience level.
Meet the PTAG Team!
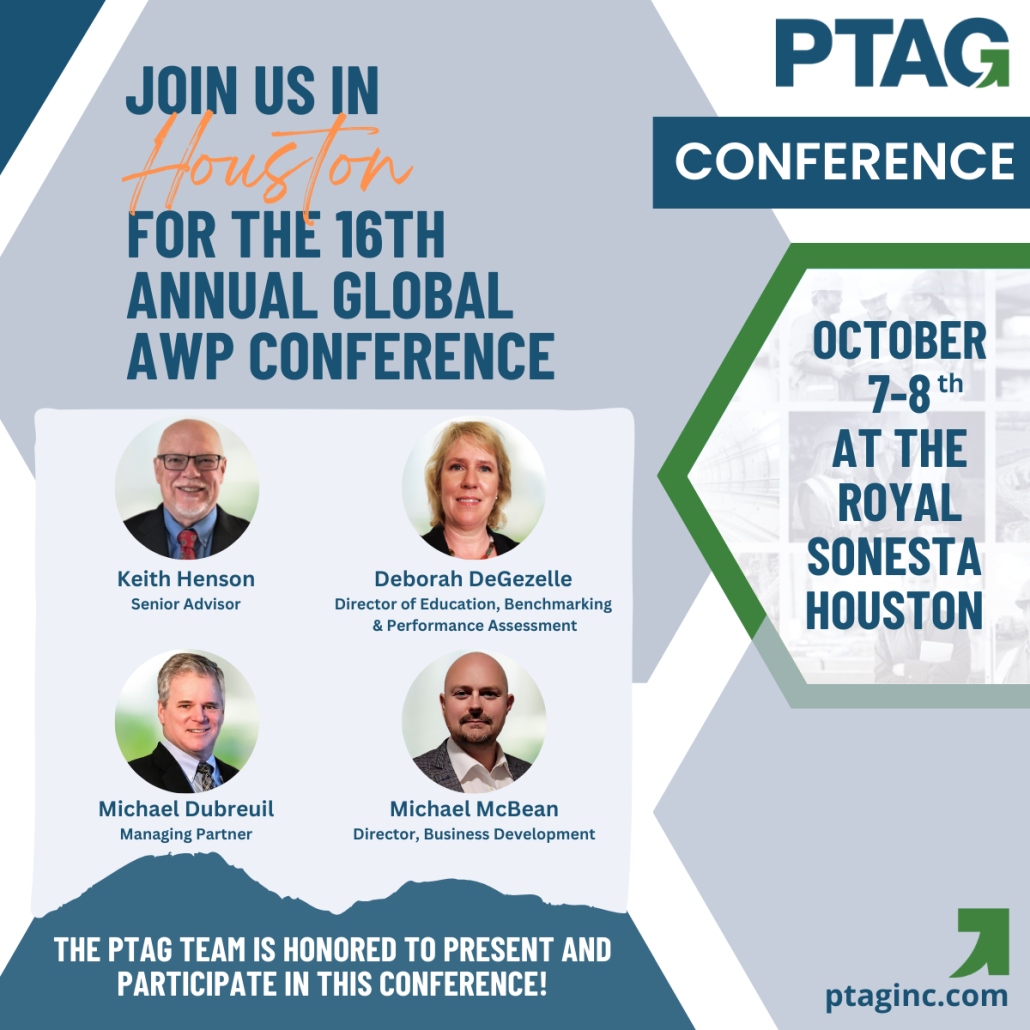
PTAG’s Michael Michael Dubreuil, Keith Henson, Michael McBean, and Deborah DeGezelle are attending the conference. Be sure to attend the following sessions where they are presenting:
Monday, October 7th, 10:00 – 11:00
Next Gen Project Delivery – Getting Started, You Can’t Afford Not To
Speakers: Michael Dubreuil, James Choo, Fernando Espana, John Strickland & Mark Childerson
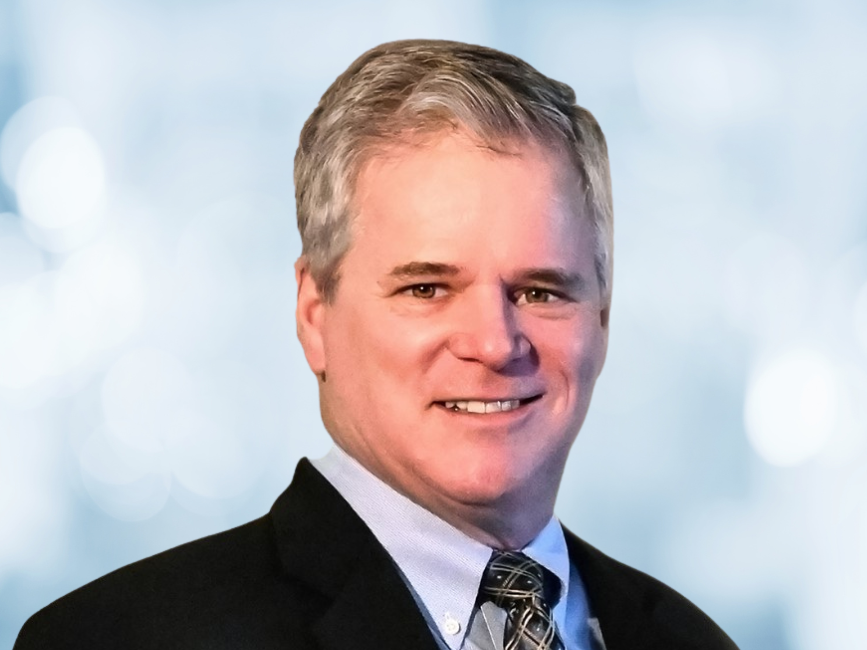
Monday, October 7th, 11:30 – 12:30
Leveraging I2PD and Lean to create flow in AWP Projects
Speaker: Keith Henson

Co-presenter: Michael McBean
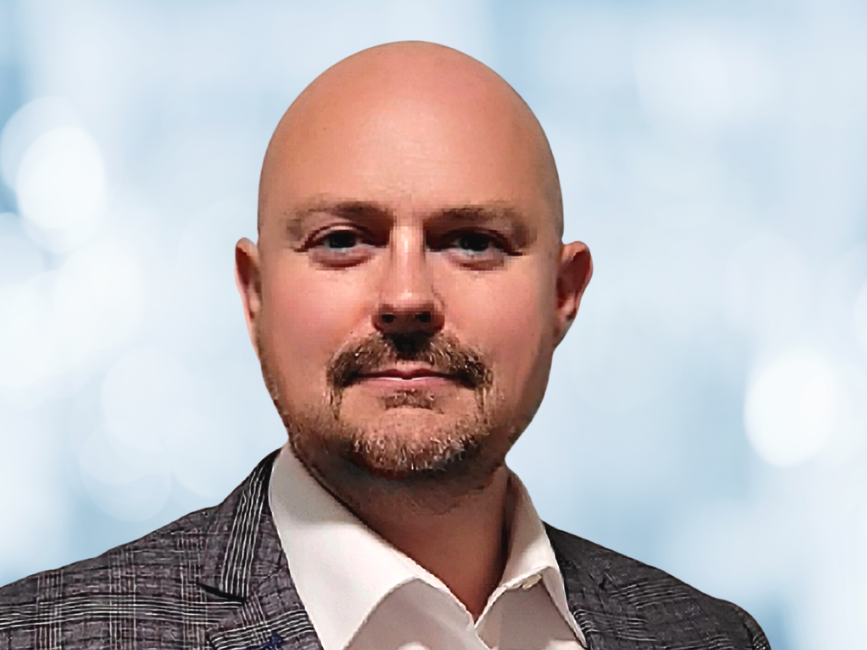
Monday, October 7th, 1:30 – 2:30
Workshop on Facilitating Process Issues -Applying Collaborative Contracting to AWP project
Speaker: Michael Dubreuil
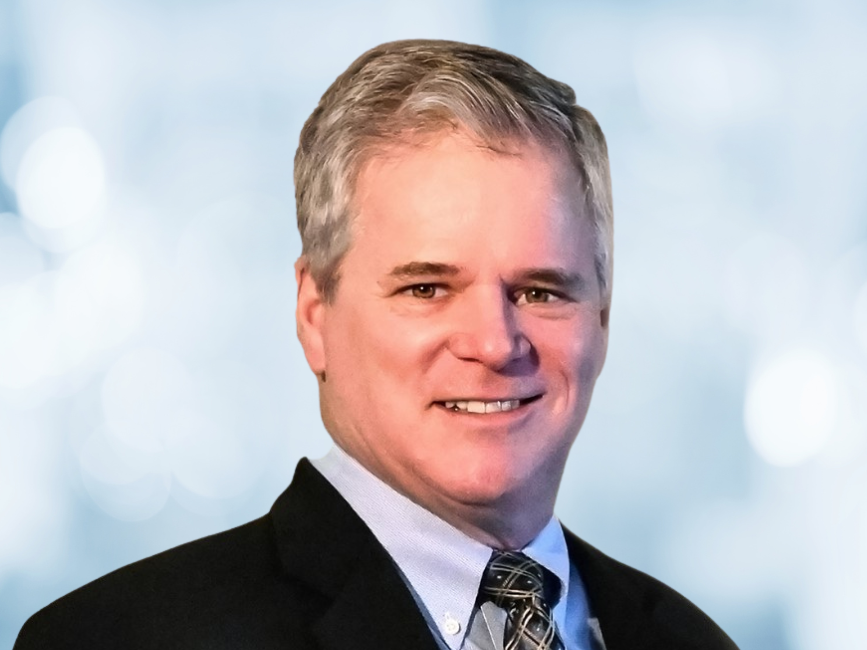
Monday, October 7th, 1:30 – 2:30
Workshop on Facilitating Process Issues – Leadership’s role in creating and maintaining a more collaborative project environment
Speaker: Keith Henson

As industry leaders in Project Management Advisory, Construction Management, Project Controls, and AWP Implementation, the PTAG team is eager to engage with fellow practitioners and share our insights on how AWP can drive project success. We look forward to discussing how PTAG’s expertise in AWP can help optimize your projects and deliver exceptional results.
By sponsoring the 16th Annual Global AWP Conference, we are reinforcing our commitment to advancing the industry and supporting the development of best practices that benefit all stakeholders.
Join Us in Houston!
We invite you to connect with us at the conference and discover how PTAG can support your AWP journey. Whether you’re interested in learning more about AWP or exploring how to optimize your project delivery, our team is here to provide insights and solutions tailored to your unique challenges.
Don’t miss this opportunity to be part of the future of construction. We look forward to seeing you in Houston!
For more information about the 16th Annual Global AWP Conference, click here!